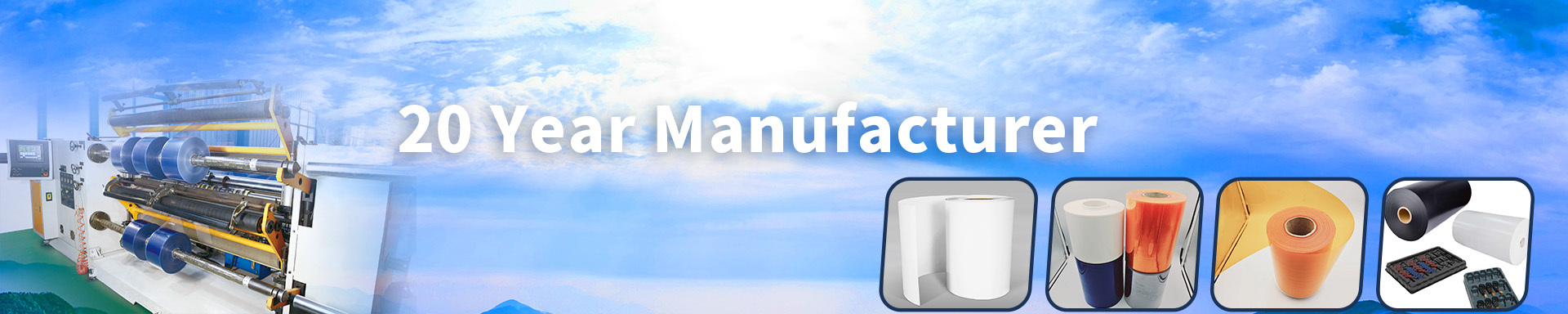
- Home
- >
- News
- >
- Product news
- >
News
Material: PET Printable sheet Thickness 0.012mm/customization Size: 100mm/Customization GRADE: Food grade film color: transparent/white/ customization location: china usage :for food packing
Material: PVC ROLL Thickness 0.45-0.018mm-customization Size: 80MM/130MM/Customization GRADE: pharma grade film color: white/ customization location: china Usage: Pharmaceutical, dried food container ,industry , engineering
Material: PET Printable sheet Thickness 0.012mm/customization Size: 100mm/Customization GRADE: Food grade film color: transparent/white/ customization location: china usage :for food PACKING , Printable packing
Material: PP Thermal formed sheet Thickness 0.25-0.9mm/customization Size: 300mm/Customization GRADE: Food grade film color: black/white/ customization location: china usage :for food tray ,mircronwave food container
Material: PC fireproofing sheet Thickness 0.18mm/customization Size: A4/Customization GRADE: Food grade film color: white/ customization location: china for food tray plant tray
Material: PP Thermal formed sheet Thickness 0.25-0.9mm/customization Size: 300mm/Customization GRADE: Food grade film color: black/white/ customization location: china usage :for food tray ,mircronwave food container
Material: PPEVOH Thermal formed sheet Thickness 0.25-0.9mm/customization Size: 300mm/Customization GRADE: Food grade film color: black/white/ customization location: china usage :for food tray ,mircronwave food container
Material: PVC ROLL Thickness 0.45-0.018mm-customization Size: 80MM/130MM/Customization GRADE:TOP grade film color: white/ customization location: china Usage: PRINTABLE FILM ,both side matte printable
Material: PVC ROLL Thickness 0.25-0.8mm-customization Size: 80MM/130MM/Customization GRADE: pharma grade film color: white/ customization location: china Usage: costmitic, wine, jewelry packing ,
Material: PVC ROLL Thickness 0.45-0.018mm-customization Size: 80MM/130MM/Customization GRADE: pharma grade film color: white/ customization location: china Usage: CEILING PANEL